Research Highlight: Investigation of last-mile grocery delivery in a suburban environment

This research project has been highlighted by VT as a Daily Video!
The objective of this investigation was to map and fully characterize the process that packaged-goods experience from the moment they are picked up from a shelf in a grocery store to when they arrive at a consumer’s doorstep. An additional goal was the identification and evaluation of the potential hazards that may occur during this process. Graduate student Joe Keller (M.S., Charlottesville, VA) was selected to lead the group of undergraduate students, Zachary Weston (Senior, Ferndale, VA), Morgan Bright (Senior, Littleton, NC), Kyle Main (Senior, Virginia Beach, VA), and Jiyu Niu (Senior, Qingdao, China) through this research project (Image 1).
Last-mile delivery for groceries has shown increased popularity in recent years. A 2019 study of U.S. residents taken during the Covid-19 pandemic showed 31% of respondents engaged in online grocery shopping, and 21% of them responded that they purchase groceries through delivery by local retailers at least once a week. An estimated 33% of the U.S. national grocery market now utilizes online delivery services, so this investigation into last-mile delivery reflects the probable outcome for a large share of grocery-type consumer packages.
The increased handling that is introduced by delivery services presents a variety of additional, potential hazards that need to be considered. In extreme cases, these hazards may yield damaged, spoilt, or otherwise compromised items. Most grocery delivery services are carried out by consumer vehicles which are built to provide a smoother, steadier ride compared to delivery trucks. Due to this, for purposes of this investigation, vibration was deemed inconsequential. Shock hazards were the primary focus of the experimental data collection. This shock data will aid in simulating the potential high-risk situations, as well as any drop scenarios, that could compromise the packaged goods. In addition, this study investigated the effects of delivery size, grocery stacking, and overtime delivery. Proper accounting of these factors during research helped to evaluate whether current packaging standards are sufficient to guarantee acceptable conditions for last-mile delivery.
In the interest of creating a general map of the delivery process, data was gathered from multiple services to account for differing approaches. To better understand the delivery handling process, four drivers and two store representatives from four different companies were interviewed on the procedures they follow from the moment the product leaves the shelf at the retailer to when it is placed at its destination by the delivery service. After gathering sufficient information regarding the handling process, we were able create an outline of the general procedure for a delivery (Image 2).

The shock data for this experiment was collected using Lansmont Saver 3D15 sensors (Image 3a) which were housed in custom, decoy corrugated containers. To account for differences in grocery item size and ensure accuracy for the sensor, two box sizes were used: one small box friction fit with foam, and one bigger metal framed box equipped with a steel frame and foam corners (Image 3b). Using these decoy boxes (Image 3c) with 3D15 sensors, eight trials, in two sets of four, were conducted at a suburban chain grocery store following the delivery process map that was outlined through the interviews.
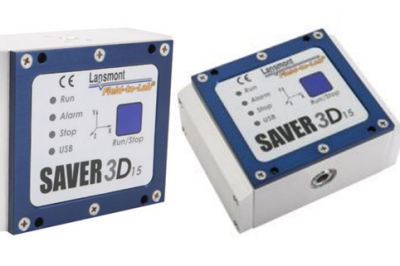

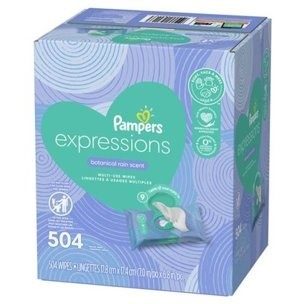
The trials each had the same delivery route and destination 2.7 miles away. The trials began when the decoy package with the activated sensor was placed in the shopping cart. During the first set of four trials, all drivers placed the groceries in the backseat of their vehicles, while the second set placed all groceries in their trunks. Alternating drivers and shoppers were used and some trials used the belt-checkout lines, while the others were placed through self-checkout. Events while driving and shopping were manually recorded with a timestamp to later compare to sensor data collected events. The trials ended when the test package was received at the doorstep and the sensor was deactivated.
To determine where products undergo the most shock events, seven orders were placed through a third-party delivery service to the same suburban grocery store chain and timed to find the average times spent in each area of the process. Event data was collected from the simulated grocery delivery trips and compiled. Notably, most of the drops that occur throughout the entire delivery route are below two inches. Significant drop heights (of greater than 3”) correspond in order of intensity and frequency with: leaving the box at the door, putting the product in the car, and putting the product in the cart. The maximum number of events that occurred in a single trip was seven and the minimum number of events were two. Common across all the trips were two events; once as the package was being placed in the cart and again when it was being placed at the customer’s door (Image 4).
The study improved our understanding of the processes involved with last mile grocery delivery that were not in focus from historical evaluations. Based on the collected shock data, it appears that last mile grocery delivery does not pose any significant hazards to packaging.